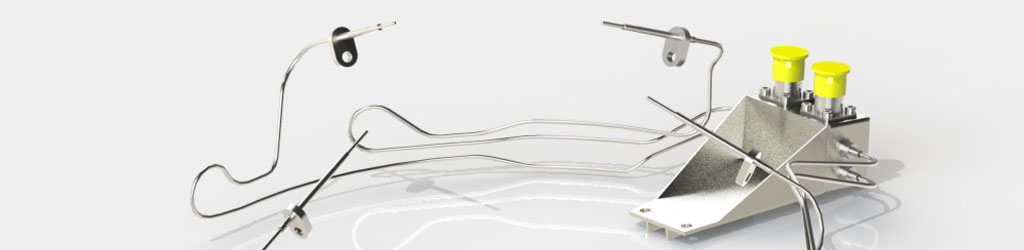
Thermocoax uses top noble metals in the manufacture of its high-temperature thermocouples for new generation aircraft gas turbines and fuel cells
When the heat is on
From compressors to turbines, from exhaust lines to test programmes, high-temperature thermocouples are an invaluable tool on the powergen market. The new generation of gas turbines is more efficient, but the extreme temperatures at which they operate demand better monitoring tools.
For airborne and ground applications, Thermocoax has a successful history of custom-building thermocouples with its proprietary mineral insulated cabling. Today we are advancing our technology to offer thermocouples that are manufactured with the most noble metals, including platinum and rhodium, for exposure to 2300°C.
All our high temperature solutions have undergone NIST calibration and can be MIL/RTCA DO160 certified for airborne applications.
Tried, Tested, and Tusted
Thermocoax is a major supplier of high temperature thermocouples for airborne applications as well as testing and qualification programmes. Our clients include Original Equipment Manufacturers in Europe and North America who are in the business of building aircraft engines, heavy duty gas turbines and solid oxide fuel cells (SOFC).
They can have complete confidence in Thermocoax, knowing that our products have reached the 24000 hour operating hours required by this industry. To date, more than 10 000 thermocouples harnesses are working on board helicopters.
Custom Solutions for Harsh Conditions
Manufactured by a dedicated team of engineers, our high-temperature thermocouples are designed for a range of applications, e.g. low and high pressure turbine, bearing, exhaust temperature monitoring and fire detection. We also offer engineering solutions for customised products, such as rake thermocouples for exhaust diffusers. And Thermocoax supplies flash-back thermocouples and Haynes 230 thermocouples to control temperatures in SOFC stacks.
As standard, the outer sheaths for our high temperature thermocouples are manufactured using Inconel and stainless steel. For cable sheaths for harsh machine conditions and specialist applications, we use Haynes® alloysfor combustion chambers, 230 for fuel cells and high-sulphur exhaust lines.
Standing by our clients at every stage
Whether to relieve stress during repairs on powergen parts or to provide heating blankets to keep powergen modules warm for installation, Thermocoax is in the business of providing heating solutions with 100% traceability of raw materials. From conception to prototype development to production, our R&D teams are equipped to meet the precise engineering needs of the aviation industry.
High-temperature Thermocouples : Technical data
Thermocouples up to 1000 degrees C
- K/N types
- Class 1
- Stainless steel/Haynes® sheaths
- 25-6 mm diameter
Thermocouples up to 2300 degrees C
- S/R/B/C type
- Platinum, rhodium, tantalum
- 7-3 mm diameter
For more detailed specifications and information about our high-temperature thermocouples, please do not hesitate to request a quote.